About us
Lee Emmons
President of Nu-Bird Inc.
On the front lines as a licensed dental hygienist in Washington State, Lee Emmons knows firsthand that necessity is the mother of invention. Forming Nu-bird Inc., Emmons is the inventor and patent owner of the Nu-Bird Suction Mirror. The Nu-Bird Suction Mirror is a Class 1 medical device used to remove water and debris out of the oral cavity while providing over 180 degrees of visibility.
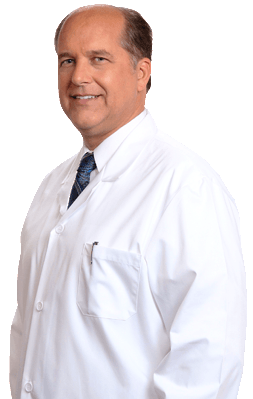
With the help of a CNC Milling machine, Emmons quickly ramped up manufacturing of the Nu-Bird Suction Mirror in less than one years’ time. “Last year, I went from building prototypes and bending copper tubing around mirrors to drilling holes just with a Dremel,” Emmons recounts. “I purchased a CNC milling machine last February and learned how to run a mill, 3D model in CAD, and create machine code. I had to stay pretty focused on exactly what it was I was doing.”
With the exception of a rhodium-coated mirror coin held at the front of the housing, Emmons manufactures the Nu-Bird Mirror entirely on his milling machine. “I make the entire housing that holds the mirror coin. The coin clicks in place and is held in position with a cross piece of stainless steel used to hold tension on the forward edge of the housing. Because it’s a front-surface mirror, you can replace it with another when it gets scratched up,” he explained.
With such careful attention to detail and superior design, Emmons has improved upon the tools available for ultrasonic dental procedures. “The super thing about the Nu-bird device is its suction capacity. To measure suction volumes, I had to build a special testing device that is almost like a little wind tunnel. Because dental equipment using suction systems vary in flow and strength, I had to take that into consideration when designing the Nu-Bird Mirror. My goal was to be able to maximize the device to the optimum capability available. This meant that everything had to be made ultra thin and it had to be bored out with as large of an inner diameter as possible.”
“The dental clinicians that have adopted and are using the Nu-Bird suction mirror in practice have been realizing it’s been cutting their time in half and has been increasing their accuracy,” Emmons said. “When you’re getting your teeth cleaned there are certain areas in the mouth that we can’t see. So, at some point hygienists and dentist are guessing and missing quite a bit. The Nu-Bird suction mirror has extended the visibility into the oral cavity and lets us work more accurately without drowning the patient.”
With the Nu-Bird Suction Mirror successfully implemented in a number of dental offices and dental schools, Emmons has made the devices available for purchase on his website. His future plans include manufacturing the Nu-Bird suction mirror out of a FDA approved polymer. Emmons is concurrently improving his machinist skills, injection molding and prototyping.